Crafting Excellence with Custom Aluminum Extrusions for Unique Project Needs
Aluminum extrusions have revolutionized the manufacturing industry, offering unparalleled versatility and strength. Whether you’re designing a simple frame or an intricate component, custom aluminum extrusions provide endless possibilities. This blog post explores the incredible benefits of tailor-made aluminum extrusion solutions, popular customization options, and how to effectively collaborate with suppliers. By the end, you’ll see real-world examples and understand the challenges and solutions involved in creating bespoke aluminum profiles.
Benefits of Tailor-Made Aluminum Extrusion Solutions
Popular Customization Options Shapes Sizes and Finishes
How to Work with Suppliers on Designing Custom Extrusions
Real-World Examples of Customized Aluminum Extrusion Projects
Challenges and Solutions in Customizing Aluminum Profiles
Benefits of Tailor-Made Aluminum Extrusion Solutions
Custom aluminum extrusions offer a host of benefits, making them an attractive choice for various industries. One significant advantage is the ability to design components that precisely meet specific project requirements. From unique shapes to specific sizes, the customization options are nearly limitless. This flexibility ensures that each piece fits perfectly within the larger assembly, reducing the need for additional modifications.Cost-efficiency is another major benefit. When components are designed to exact specifications, material waste is minimized, and production processes become more streamlined. This can lead to significant cost savings, particularly for large-scale projects. Additionally, custom aluminum extrusions are highly durable and lightweight, making them ideal for applications where weight is a critical factor.Beyond functionality, custom aluminum extrusions also offer aesthetic benefits. With various finishing options available, these extrusions can be tailored to enhance the visual appeal of the final product. Whether it’s a sleek, polished look or a rugged, textured finish, the right customization can elevate the overall design.
Popular Customization Options Shapes Sizes and Finishes
When it comes to custom aluminum extrusions, the options are vast. One of the most common customization choices involves the shape of the extrusion. Whether you need complex geometric designs, hollow sections, or intricate patterns, aluminum can be molded to meet these needs. This level of precision is invaluable in creating components that integrate seamlessly into your projects.Customization doesn’t stop at shapes. Sizes can be tailored to fit exact dimensions, ensuring that each piece meets the unique requirements of your project. This is particularly beneficial for industries such as construction and automotive, where precise measurements are crucial for structural integrity and performance.Finishing options further enhance the versatility of custom aluminum extrusions. From anodizing and powder coating to brushing and polishing, there are numerous ways to achieve the desired look and feel. These finishes not only improve the aesthetic appeal but also provide additional protection against environmental factors, extending the lifespan of the components.
How to Work with Suppliers on Designing Custom Extrusions
Collaborating with suppliers is a critical step in the process of designing custom aluminum extrusions. The first step is to communicate your project requirements clearly. Provide detailed specifications, including dimensions, shapes, and any specific finishing options you desire. This helps suppliers understand your vision and ensures that they can deliver precisely what you need.Engaging in early discussions with suppliers can also be beneficial. Their expertise can provide valuable insights into the feasibility of your designs and suggest potential improvements. This collaborative approach can lead to more efficient production processes and higher-quality outcomes.Regular communication throughout the project is essential. Keeping suppliers updated on any changes or adjustments can help prevent delays and ensure that the final product meets your expectations. Building a strong relationship with your suppliers fosters trust and encourages a more seamless and productive collaboration.
Real-World Examples of Customized Aluminum Extrusion Projects
Customized aluminum extrusions have been successfully implemented in numerous projects across various industries. One notable example is the use of custom extrusions in the construction of modern architectural structures. These extrusions provide the flexibility to create unique designs while ensuring structural stability and durability.In the automotive industry, custom aluminum extrusions are used to manufacture lightweight yet robust components. This includes everything from chassis parts to interior trim, contributing to the overall efficiency and performance of vehicles. The ability to customize these components allows manufacturers to achieve optimal weight distribution and enhance the driving experience.Another fascinating application of custom aluminum extrusions is in the electronics industry. Heat sinks, for example, are often created using custom extrusions to ensure efficient thermal management. The precise design and size of these extrusions enable effective heat dissipation, critical for the performance and longevity of electronic devices.
Challenges and Solutions in Customizing Aluminum Profiles
While the benefits of custom aluminum extrusions are clear, the process does come with its challenges. One common issue is the complexity of designing intricate shapes. Advanced CAD software and skilled engineers are essential to overcome this challenge, ensuring that designs are both feasible and functional.Material selection is another critical factor. Different aluminum alloys offer varying properties, such as strength, corrosion resistance, and machinability. Choosing the right alloy for your specific application is crucial to achieving the desired performance and longevity of the components.Production costs can also be a concern, particularly for small-scale projects. However, working closely with suppliers to optimize design and production processes can help mitigate these costs. Additionally, the long-term benefits of custom aluminum extrusions, such as reduced material waste and improved efficiency, often outweigh the initial investment.
In conclusion, custom aluminum extrusions offer a multitude of benefits, from precise design and cost-efficiency to enhanced aesthetics and durability. By understanding the various customization options and effectively collaborating with suppliers, businesses can leverage these advantages to create innovative and high-quality products. Despite the challenges involved, the solutions provided by experienced suppliers and advanced technologies make it possible to achieve exceptional results. If you’re ready to explore the possibilities of custom aluminum extrusions for your next project, don’t hesitate to get in touch with your trusted supplier today.
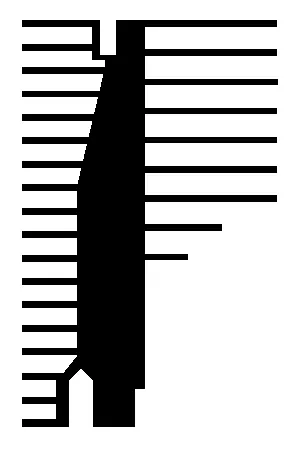
Comments
Post a Comment