Why Magnetic Flux Leakage is the Future of Non-Destructive Testing
In an era where infrastructure and manufacturing demand top-notch quality and reliability, non-destructive testing (NDT) has become indispensable. Traditional inspection methods often involve invasive procedures that can harm the material being tested. Enter Magnetic Flux Leakage (MFL), a revolutionary technique transforming how industries inspect and maintain their assets.
Table of contents:
How MFL Technology is Evolving to Meet Industry Demands
The Role of MFL in Advancing Non-Destructive Testing for Infrastructure and Manufacturing
The Advantages of Using MFL for Accurate and Non-Invasive Inspections
The Future of Non-Destructive Testing: Innovations in Magnetic Flux Leakage
This blog post aims to explore the evolution of MFL technology, its role in advancing NDT, and the advantages it offers for accurate and non-invasive inspections.
How MFL Technology is Evolving to Meet Industry Demands
Magnetic Flux Leakage technology has come a long way from its inception. Initially used for basic metal inspections, Magnetic Flux Leakage (MFL) has evolved into a sophisticated tool capable of detecting even the minutest defects. The advancements in sensor technology, data processing algorithms, and portable devices have significantly enhanced the accuracy and efficiency of Magnetic Flux Leakage (MFL). Companies like Tianjin Ruicheng Testing Technology have been at the forefront, developing high-precision metal crack detectors and longitudinal probe brackets that offer superior signal sensitivity and signal-to-noise ratios. These innovations ensure that MFL remains a reliable and efficient method for non-destructive testing, meeting the growing demands of various industries.
The Role of MFL in Advancing Non-Destructive Testing for Infrastructure and Manufacturing
Magnetic Flux Leakage (MFL) is playing a pivotal role in advancing non-destructive testing for both infrastructure and manufacturing sectors. For infrastructure, MFL is invaluable for inspecting pipelines, bridges, and other critical structures without causing any damage. In manufacturing, Magnetic Flux Leakage (MFL) aids in quality control by detecting defects in raw materials and finished products. The ability of Magnetic Flux Leakage (MFL) to provide real-time data and instant feedback makes it an essential tool for ensuring the integrity and longevity of assets. Companies can now perform regular inspections with minimal downtime, thanks to portable seamless Magnetic Flux Leakage (MFL) detectors that are easy to use and highly effective.
The Advantages of Using MFL for Accurate and Non-Invasive Inspections
One of the most significant advantages of Magnetic Flux Leakage is its non-invasive nature. Unlike traditional methods that may require cutting or dismantling parts of the asset, Magnetic Flux Leakage (MFL) can detect defects without causing any damage. This feature is particularly beneficial for industries where maintaining structural integrity is crucial. Additionally, MFL offers exceptional accuracy in detecting surface and sub-surface defects, ensuring comprehensive inspections. The high sensitivity and precision of MFL detectors, such as those developed by Tianjin Ruicheng Testing Technology, make them ideal for a wide range of applications. Furthermore, the portability and ease of use of modern Magnetic Flux Leakage (MFL) devices enhance their practicality, allowing for quick and efficient inspections in various settings.
The Future of Non-Destructive Testing: Innovations in Magnetic Flux Leakage
As technology continues to advance, the future of Magnetic Flux Leakage (MFL) is poised to bring even more innovative solutions to the field of non-destructive testing. Emerging trends include the integration of artificial intelligence and machine learning into MFL systems, enabling real-time data analysis and intelligent defect identification. This will not only enhance the accuracy of inspections but also allow for predictive maintenance, where potential issues can be identified before they become critical. Additionally, developments in micro-sensor technology are paving the way for the creation of smaller, more efficient MFL devices that can access previously unreachable inspection points. Furthermore, as industries increasingly embrace digital transformation, the incorporation of Internet of Things (IoT) capabilities into MFL technology will enable seamless connectivity and data sharing, further streamlining the inspection process. These innovations signify a promising future for MFL, ensuring that it remains at the forefront of non-destructive testing methodologies.
Magnetic Flux Leakage is undeniably shaping the future of non-destructive testing. Its ability to provide accurate, real-time, and non-invasive inspections makes it an invaluable asset for industries aiming to maintain high standards of quality and safety. With continuous advancements and innovations, MFL technology is set to become even more integral to NDT processes. For those looking to integrate cutting-edge non-destructive testing (NDT) solutions into their operations, exploring the potential of MFL is a must. If you're interested in learning more about how MFL can benefit your business, consider reaching out to industry leaders like Tianjin Ruicheng Testing Technology, who offer professional non-destructive testing technical services tailored to meet your needs.
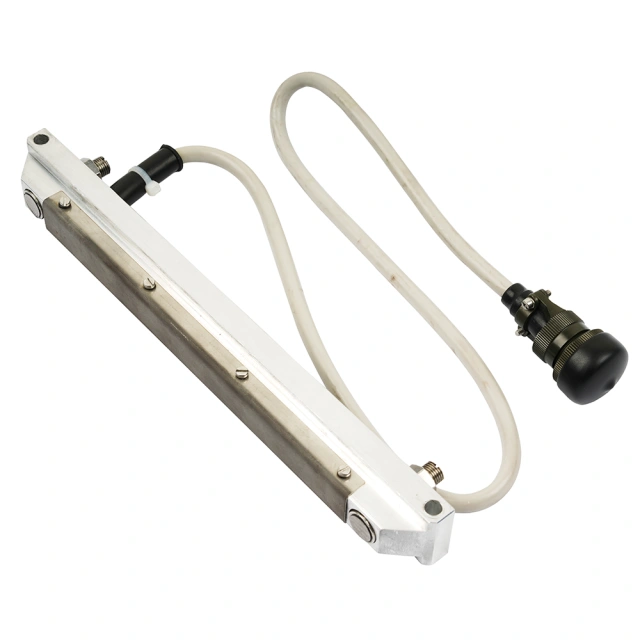
Comments
Post a Comment