Enhancing Performance with Advanced Grinding Wheel Technologies
For industries reliant on metalworking processes, grinding wheels have become indispensable tools. Over the years, advancements in grinding technology have revolutionized efficiency and precision in this field, with one-dimensional abrasive wheels evolving into expertly engineered solutions. Among these innovations, Precision-Shaped Grain (PSG) technology has emerged as a standout feature, significantly influencing grinding wheel capabilities. Today, leading grinding wheel suppliers are incorporating PSG into their products to meet the growing demand for enhanced durability, reduced material waste, and lower operating costs. From the array of new advancements, this blog sheds light on the role advanced grinding wheel technologies play in metalworking efficiency, especially focusing on PSG technology.
Table of contents:
Introduction to Precision-Shaped Grain (PSG) Technology
Benefits of PSG in Depressed Center Grinding Wheels
Case Studies Demonstrating Increased Efficiency and Longevity
Future Trends in Abrasive Material Development
Introduction to Precision-Shaped Grain (PSG) Technology
PSG technology has shifted the dynamic of grinding wheel performance by incorporating precisely engineered ceramic grain structures. Unlike conventional abrasives, PSG is designed to maintain a sharp cutting edge throughout its usage. This characteristic increases the tool’s efficiency while controlling excessive wear, ensuring that users consume fewer abrasives over time. Leading companies like grinding wheels suppliers and manufacturers of 4” cut-off wheels or 7" grinding wheels are now leveraging PSG’s ability to maintain fine grain edges during intense operations. For applications requiring fine grinding or removing excess metal, PSG-integrated wheels ensure an elevated cutting rate while minimizing material grain deformation.Furthermore, PSG technology emphasizes eco-friendliness, as the reduced consumption of abrasives aligns with efforts to lower industrial waste. By providing a consistent grinding performance over extended durations, companies experience improved output and reduced downtime. Incorporating this advanced technology would undeniably enhance efficiency for enterprises heavily dependent on applications like cutting steel pipelines or smoothing general cast iron moldings.
Benefits of PSG in Depressed Center Grinding Wheels
Depressed center grinding wheels are known for their versatility in metal polishing, cutting, and grinding applications, and the addition of PSG components enhances these benefits, creating more user-friendly and cost-effective solutions. Leading brands, like abrasives grinding wheels suppliers, provide tailored products utilizing this technology to deliver key advantages. These include durability, as PSG-equipped cutting tools are designed to withstand extreme pressure without cracking, reducing replacements and improving reliability during long grinding sessions. Safety features are also prioritized, with PSG-based grinding wheels, such as those from premium 7" grinding wheels manufacturers, often reinforced with cross-fiber reinforcements to ensure impact resistance and safer handling. Additionally, PSG minimizes material loss, reducing unnecessary consumption and costs while promoting environmental sustainability. Lastly, operator fatigue is reduced through ergonomic designs that require less pressure, as highlighted by brands like Fuji Grinding Wheel, ensuring smoother handling and a better user experience during extended use.
Case Studies Demonstrating Increased Efficiency and Longevity
Within varied industries, PSG-backed grinding wheels excel across a range of operations. Let's consider an oft-discussed 4” cut-off wheels manufacturer whose product was deployed in automotive assembly lines. The purpose was to enhance the efficiency of cutting thin metal sheets designed for automobile panels. Immediately, plant supervisors reported over 30% better cutting speeds than traditional grinding wheels without PSG. Additionally, the employee downtime caused by tool switching was cut in half due to the extended lifespan of the grinding wheels.A 7" grinding wheels manufacturer, focusing on structural engineering projects, further provided insights into PSG technology benefits during steel beam construction. The requirement for grinding heavy gauge metals such as cast iron often resulted in overheating damage to traditional abrasive wheels. However, installing PSG grinding wheels eliminated instances of wheel burnout, ensuring longer service durations even under high-friction scenarios. Such real-world results consistently reaffirm the long-term advantages of investing in PSG-led grinding solutions for industrial applications.
Future Trends in Abrasive Material Development
Looking forward, abrasive tool manufacturers are shifting towards global compliance in safety and sustainability standards. Expect innovation in grinding wheel customization, with features such as self-regenerating abrasive grains becoming staples within new offerings. Beyond mere durability, the next generation of abrasive tools will focus on AI-driven predictive analytics to customize conditions such as grain wear evaluation, cutting rates, or load performance tracking.Regional and global grinding wheels suppliers must invest in automated production techniques to maintain competitiveness. Brands currently considered trusted suppliers of the best angle grinder wheels for cutting metal are leaning toward hybrid abrasive designs that combine PSG with flexible grinding wheel structures.Ultimately, the integration of enhanced safety, sustainability, and technological innovations is set to redefine abrasive products for both niche requirements and mass-metalworking tasks.
Whether you're in manufacturing, construction, or automotive assembly, the right grinding tools make all the difference. By integrating innovations like PSG technology into premium grinding wheels, suppliers are elevating the standard for metalworking tools. Consistent material removal rates, optimized operator safety, and reduced operational costs ensure that investing in state-of-the-art grinding technologies isn't just about faster cuts—it's about smarter, more sustainable operations.Looking for grinding wheels that combine functionality with cutting-edge technology? Connect with the experts. Get your perfect grinding wheel solution today!
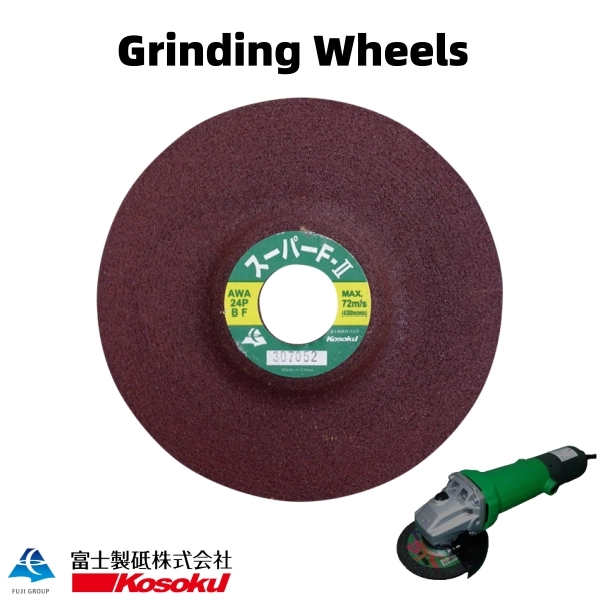
Comments
Post a Comment