The Importance of Quality Assurance in Solar Mounting System Manufacturing
Quality assurance (QA) has become the backbone of industries focusing on renewable energy, especially in solar mounting system manufacturing. For products like Flat Roof Solar Mounting Systems, reliable performance and long-term durability are vital—these systems must endure varying weather conditions while supporting photovoltaic (PV) panels. Without rigorous quality control, systems can fail, resulting in inefficient energy production, increased costs, and loss of trust in solar solutions. This post explores the critical role of quality assurance, shedding light on key practices like rigorous testing, adherence to international standards, leveraging customer feedback, and achieving important certifications and accreditations.
Table of contents:
Implementing Rigorous Testing Protocols
Adhering to International Quality Standards
Continuous Improvement Through Customer Feedback
Certifications and Accreditations in Manufacturing
Implementing Rigorous Testing Protocols
Durable Flat Roof Solar Mounting Systems require consistent, thorough testing throughout the manufacturing process. Testing protocols play a crucial role in ensuring systems can withstand high wind loads, heavy snowfalls, and extreme temperatures. For example, wind resistance up to 50m/s and snow load tolerance of 2Kpa are key specifications that manufacturers routinely test for. Furthermore, testing individual components—such as racking, brackets, and cement foundations—ensures their strength and compatibility before being assembled. Advanced materials like Mg-Al-Zn coatings must also be tested for long-term corrosion resistance. Such comprehensive testing before and after assembly minimizes room for imperfections, bolsters reliability, and reduces failures, providing confidence to contractors and system owners investing in solar solutions.
Adhering to International Quality Standards
Adherence to international quality standards ensures that solar mounting systems meet global benchmarks for safety and efficiency. Standards such as AS/NZS 11710 and JISC8955-2017 serve as the foundation for Flat Roof Solar Mounting Systems, dictating design specifications that safeguard against environmental challenges. These benchmarks apply from raw material selection to the final product, providing assurance of consistency in quality. Flat roof systems that align with strict international standards not only guarantee operational stability but also make these systems viable for use in diverse regions and weather conditions. By meeting globally recognized standards, manufacturers open doors to broader markets, making renewable energy accessible to more people.
Continuous Improvement Through Customer Feedback
The solar industry thrives on adaptability, and customer feedback is an invaluable resource for continuous improvement. Customers using solar mounting systems often encounter challenges that manufacturers may not previously have anticipated. From discovering installation inefficiencies to recognizing stress points under specific environmental loads, end-user reports offer actionable insights. Collecting and analyzing customer feedback should be a priority for manufacturers, helping them address flaws in existing models and integrate suggested improvements into future designs. This iterative process not only perfects product quality over time but also strengthens trust and fosters positive relationships with customers. Businesses equipped with actionable, data-backed insights stay ahead of competitors by quickly evolving alongside client expectations.
Certifications and Accreditations in Manufacturing
Obtaining certifications and accreditations demonstrates commitment to the highest quality standards, further establishing credibility in the competitive solar market. Certifications signify that a solar mounting system has passed stringent evaluations for performance, durability, and safety. For instance, manufacturers supplying Flat Roof Solar Mounting Systems backed by internationally recognized certifications boost buyers’ confidence, signaling that the systems can operate reliably for their expected service life of 25 years. Accreditation also assures customers and contractors about compliance with environmental and ethical practices—a growing concern across industries. Additionally, certifications incentivize manufacturing excellence, ensuring companies continuously enhance the processes that bring their products to market.
Neglecting proper QA in manufacturing solar mounting systems can lead to weakened structures, underperformance, or even hazardous failures. Beyond ensuring functionality, quality-focused production also maximizes system longevity, creates energy-efficient outcomes, and builds a reputation for eco-conscious innovation. Comprehensive QA processes substantially reduce risks while improving performance, helping customers save costs and trust renewable energy solutions. Manufacturers prioritizing quality assurance stand to strengthen the solar industry as a whole, ensuring that reliable, sustainable energy is accessible for decades to come.
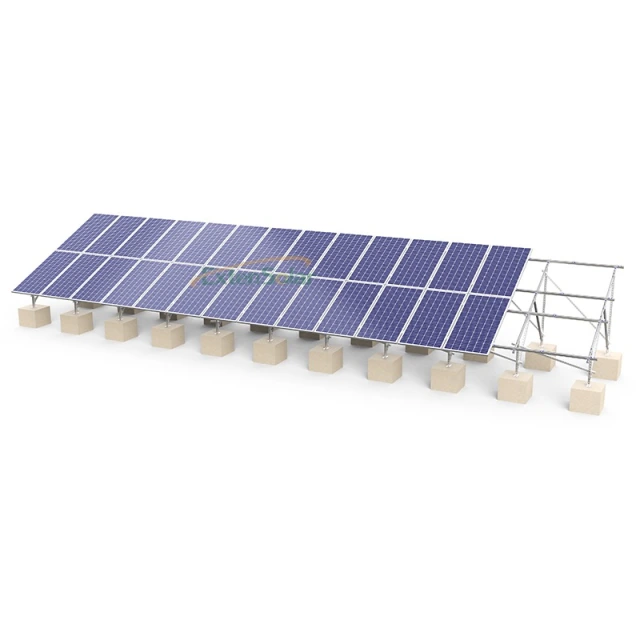
Comments
Post a Comment