Why Stainless Steel Socket Cap Screws Are Essential for Industrial Applications
Stainless steel socket cap screws serve as indispensable components in modern industrial applications. Engineered for strength, precision, and exceptional durability, these fasteners have become a preferred choice across sectors like automotive, aerospace, and heavy machinery. With the advent of high-precision designs and specialized manufacturing standards, wholesale socket cap screws now play a critical role in ensuring the reliability and efficiency of industrial operations. This blog explores their role, benefits, and the importance of precision engineering in industrial fasteners.
Table of contents:
The Role of Stainless Steel Socket Cap Screws in Industrial Machinery
Key Benefits of Using Stainless Steel for Socket Cap Screws
Why Precision Engineering Matters for Industrial Fasteners
The Role of Stainless Steel Socket Cap Screws in Industrial Machinery
Stainless steel socket cap screws are integral to industrial machinery, providing secure fastening solutions for complex assemblies. Their fully threaded design ensures uniform grip along the length of the shaft, making them ideal for applications requiring consistent clamping force. From die-fixturing to machine parts, these screws offer unparalleled reliability. Commonly featuring a hexagonal recess for easy tightening and loosening using an Allen wrench, they improve assembly efficiency while reducing equipment downtime. What makes these screws stand out is their adaptability. Socket cap screws are often used in high-stress environments, as their stainless steel construction resists corrosion and wear. Industries like automotive, where safety and precision are paramount, and aerospace, where lightweight but strong materials are essential, rely heavily on these fasteners. Additionally, applications in equipment requiring aesthetic finishes, such as consumer-facing machinery, benefit from the polished and clean appearance of stainless steel socket cap screws.
Key Benefits of Using Stainless Steel for Socket Cap Screws
Opting for stainless steel as the primary material brings a host of benefits to socket cap screws. Firstly, stainless steel offers exceptional resistance to corrosion. This is particularly important in harsh industrial environments exposed to moisture, chemicals, and varying temperatures. It minimizes maintenance needs, thereby extending equipment life. Another key advantage is strength. Stainless steel is known for its high tensile strength, which ensures that the screws can withstand significant loads without deformation or failure. This makes stainless steel socket cap screws an excellent choice for machinery that operates under high pressure or tension. Versatility is another feature worth noting. Socket cap screws made from stainless steel are available in a variety of finishes, dimensions, and head types, making them adaptable to unique industrial requirements. Furthermore, their inherent properties ensure that the screws maintain their structural integrity even in extreme conditions, such as those involving heat and vibration. Durability extends beyond physical attributes. The longevity of stainless steel socket cap screws contributes to cost-effectiveness as businesses save money on frequent replacements. Since these screws are ANSI/ASME B18.3 compliant, manufacturers can ensure their fasteners meet internationally recognized standards for safety and performance.
Why Precision Engineering Matters for Industrial Fasteners
The importance of precision engineering in manufacturing stainless steel socket cap screws cannot be understated. Precision ensures that these fasteners meet exact specifications, achieving the perfect balance between performance and reliability. Industrial equipment often involves complex designs where even minor inconsistencies in fasteners can lead to catastrophic failures. Accurate threading, uniform diameter, and precise head dimensions guarantee optimal fit and function, reducing the risk of misalignment or loosening. Precision engineering also enables customization, a crucial factor for industries with unique requirements. Custom stainless steel socket cap screws can be tailored to meet specific dimensions, materials, and coatings, ensuring enhanced compatibility and performance for niche applications. This flexibility allows industries such as telecommunications or medical technology to optimize their designs while maintaining structural robustness. At the core of precision engineering lies compliance with standards like ANSI/ASME B18.3. Adhering to these regulations guarantees that socket cap screws meet strict quality criteria, offering companies peace of mind. High-precision manufacturing processes also translate to a superior surface finish, which enhances not only the appearance of the screws but also their resistance to wear and tear.
Stainless steel socket cap screws are vital components in modern industrial applications, offering strength, corrosion resistance, and versatility. Precision engineering ensures these fasteners deliver exceptional performance, reliability, and durability. By selecting high-quality screws from a trusted screws manufacturer, industries can reduce maintenance costs, enhance operational efficiency, and ensure safety in even the toughest conditions. From automotive to aerospace and heavy machinery, screws manufacturers continue to drive industrial innovation with reliable, high-performance fasteners.
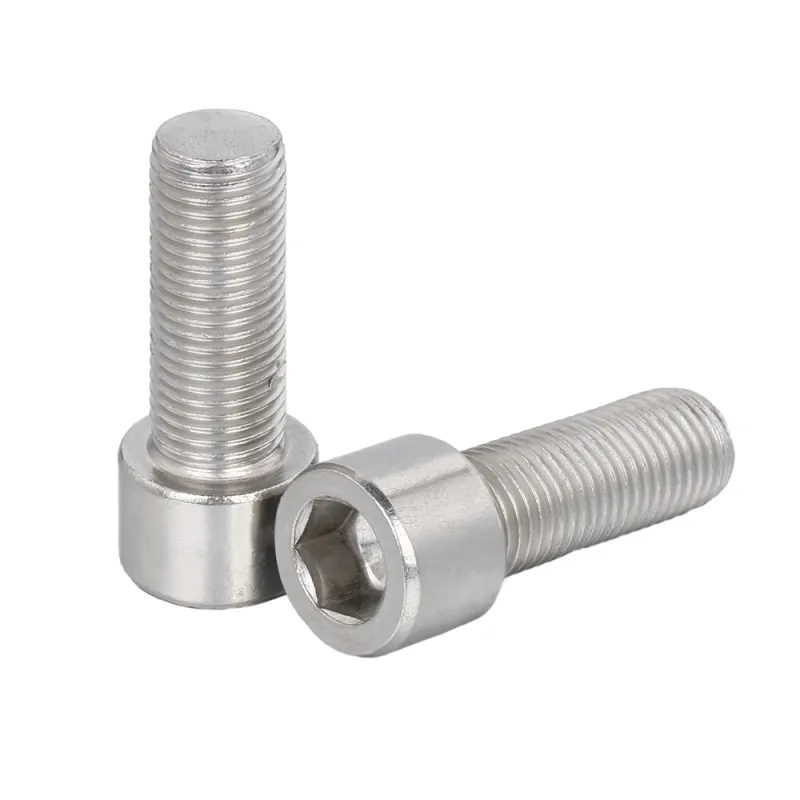
Comments
Post a Comment