Hydroxypropyl Cellulose vs. HPMC Which One is Right for You?
In the world of industrial and pharmaceutical applications, choosing the right additives can make all the difference in product performance and quality. Two popular choices are hydroxypropyl cellulose and hydroxypropyl methylcellulose (HPMC). While they might sound similar, their properties and applications vary significantly. This blog post dives deep into the differences between hydroxypropyl cellulose and HPMC to help you make an informed decision for your needs.
Table of contents:
Comparing the Properties of Hydroxypropyl Cellulose and HPMC Hydroxypropyl Methylcellulose
The Unique Benefits of Hydroxypropyl Methylcellulose in Industrial Applications
How to Choose Between Hydroxypropyl Cellulose and HPMC for Your Needs
Key Applications of Hydroxypropyl Cellulose vs. Hydroxypropyl Methylcellulose
Comparing the Properties of Hydroxypropyl Cellulose and HPMC Hydroxypropyl Methylcellulose
Hydroxypropyl cellulose and hydroxypropyl methylcellulose are both cellulose derivatives, but their chemical structures and properties differ. Hydroxypropyl cellulose is a water-soluble polymer that is highly versatile, with applications ranging from pharmaceuticals to food products. It is known for its excellent film-forming capabilities and high solubility in both water and organic solvents. On the other hand, HPMC, or hydroxypropyl methylcellulose, is a non-ionic cellulose ether that is also water-soluble. It is commonly used in construction materials, pharmaceuticals, and food products. HPMC is appreciated for its thickening, emulsifying, and stabilizing properties, making it a go-to choice in many industrial applications.
The Unique Benefits of Hydroxypropyl Methylcellulose in Industrial Applications
Hydroxypropyl methylcellulose stands out in industrial applications due to its unique properties. Its excellent water retention capabilities make it ideal for use in construction materials like cement and plaster. HPMC improves the workability of these materials, providing better adhesion and reducing the risk of cracks. Additionally, HPMC is used in various coatings and paints, where its film-forming properties enhance the durability and appearance of the final product. In the pharmaceutical industry, HPMC plays a crucial role as a binder and release agent in tablet formulations, ensuring consistent drug release and improving patient compliance.
How to Choose Between Hydroxypropyl Cellulose and HPMC for Your Needs
Choosing between hydroxypropyl cellulose and HPMC depends on your specific application and requirements. If you need a versatile, water-soluble polymer with excellent film-forming properties, hydroxypropyl cellulose is a great choice. It is particularly useful in applications where both water and organic solvent solubility are required. However, if your application demands superior water retention, thickening, and stabilizing properties, HPMC is the better option. Its non-ionic nature and high compatibility with other ingredients make it suitable for a wide range of industrial and pharmaceutical applications.
Key Applications of Hydroxypropyl Cellulose vs. Hydroxypropyl Methylcellulose
Hydroxypropyl cellulose finds its primary applications in pharmaceuticals, where it is used as a binder, film-former, and controlled-release agent. It is also employed in food products as a thickener and stabilizer, as well as in personal care products like shampoos and lotions for its film-forming and moisturizing properties. HPMC, on the other hand, is widely used in construction materials, where it enhances the workability and durability of cement, plaster, and mortar. It is also a key ingredient in coatings, paints, and adhesives, providing improved consistency and performance. In the pharmaceutical industry, HPMC is essential for controlled-release formulations and as a binder in tablet production.
Understanding the differences between hydroxypropyl cellulose and HPMC is crucial for selecting the right additive for your specific needs. While both polymers offer unique benefits, their applications and properties vary. By considering factors such as solubility, film-forming capabilities, water retention, and compatibility with other ingredients, you can make an informed decision that enhances your product's performance and quality. For more detailed information and personalized guidance, consider reaching out to industry experts or consulting with suppliers who specialize in these cellulose derivatives.
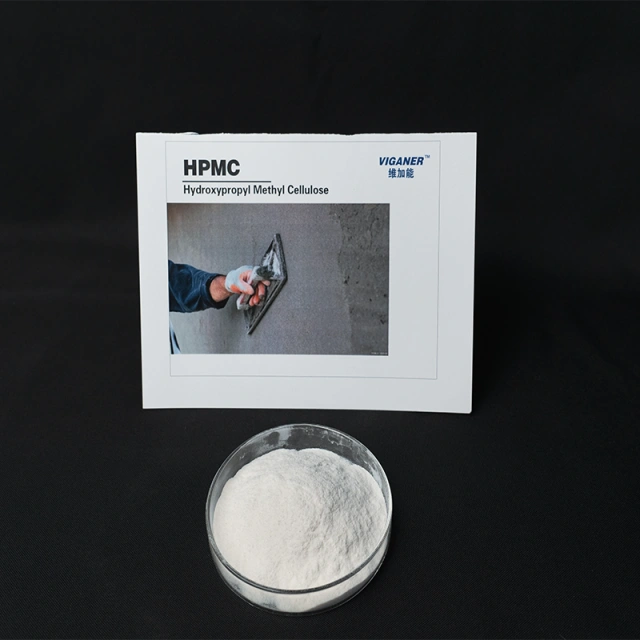
Comments
Post a Comment