Why Non-Destructive Testing with Magnetic Flux Leakage (MFL) Technology is Critical for Safety and Compliance
Non-destructive testing (NDT) has become an indispensable practice for modern industries that rely on the structural integrity, safety, and performance of materials. Among the various methods available, Magnetic Flux Leakage (MFL) testing stands out as a robust solution for identifying potential material defects, particularly in steel pipes and other metallic structures. This blog highlights the critical role MFL testing plays in preventing failures, ensuring compliance, and driving operational efficiency.
Table of contents:
How Magnetic Flux Leakage Testing Helps Prevent Equipment Failures
Comparing MFL Testing with Other Non-Destructive Testing Methods
How Magnetic Flux Leakage Testing Contributes to Risk Management in Industrial Operations
How Magnetic Flux Leakage Testing Helps Prevent Equipment Failures
Magnetic Flux Leakage Testing is key to preventing equipment failures and ensuring the safety of operations within various industries. This cutting-edge technology works by magnetizing the material being tested and identifying leaks in the magnetic field that indicate defects such as cracks or corrosion. The method is widely used for evaluating the condition of steel pipes, seamless tubes, and structural components subjected to high operational stress. Early detection of flaws through MFL testing prevents catastrophic equipment failures that could lead to accidents, production downtime, and costly repairs. Another advantage of MFL testing is its adaptability. Companies like Tianjin Ruicheng Testing Technology provide advanced MFL testing equipment that is designed to address technical issues like aging systems and insufficient repair capabilities. Their solutions are tailored to meet varied working conditions, ensuring improved detection performance and extended service life of testing equipment. Furthermore, features like recordable detection waveforms and an intuitive interface make MFL an operationally efficient and user-friendly tool for industries like oil and gas, construction, and manufacturing.
Comparing MFL Testing with Other Non-Destructive Testing Methods
MFL testing is one of many non-destructive testing methods, but it offers distinct advantages. Compared to ultrasonic testing (UT), MFL is faster and easier to use for large surfaces like pipelines. Unlike visual or dye penetrant testing, it doesn’t require direct visibility or extensive surface prep, making it ideal for harsh environments. Radiographic testing, which uses radiation, requires strict safety measures, while MFL provides a safer alternative with precise results. MFL also uniquely detects both surface and sub-surface defects, catching small irregularities often missed by other methods. Additionally, wholesale magnetic flux leakage equipment offers higher sensitivity and a better signal-to-noise ratio than foreign alternatives, as noted by suppliers like Tianjin Ruicheng Testing Technology. These advantages make MFL testing a top choice for industries needing reliable and high-performance tools.
How Magnetic Flux Leakage Testing Contributes to Risk Management in Industrial Operations
From a broader perspective, MFL testing plays a vital role in industrial risk management by enhancing safety measures and compliance protocols. Regulatory standards across industries demand thorough inspections of critical infrastructure to minimize risks associated with material failure. Failure to comply with these standards can result in hefty fines, damaged reputations, and operational halts. This is where non-destructive testing equipment, such as MFL technology, becomes a necessity. By proactively detecting potential issues, Magnetic Flux Leakage Testing helps organizations take preventative measures that protect workers, equipment, and the environment. For instance, oil and gas companies rely on MFL testing to maintain the integrity of pipelines, preventing leaks and mitigating environmental disasters. Similarly, the transportation industry uses MFL testing to ensure the structural soundness of railway tracks and vehicle components, minimizing the risks associated with wear and tear.
Magnetic Flux Leakage Testing has revolutionized the way industries approach safety, reliability, and compliance. The technology’s ability to prevent equipment failures, outperform other testing methods, and reduce operational risks has made it a critical tool for businesses worldwide. Suppliers like Tianjin Ruicheng Testing Technology provide solutions that not only meet but exceed industry expectations, offering high-performance equipment tailored to specific challenges. Whether you're looking for wholesale magnetic flux leakage testing equipment or seeking advanced non-destructive testing tools for seamless steel pipes, MFL technology is an investment in the safety, efficiency, and future-proofing of your operations. With features like recordable detection waveforms and customizable solutions, the next generation of MFL testing is poised to set even higher standards for industrial applications.
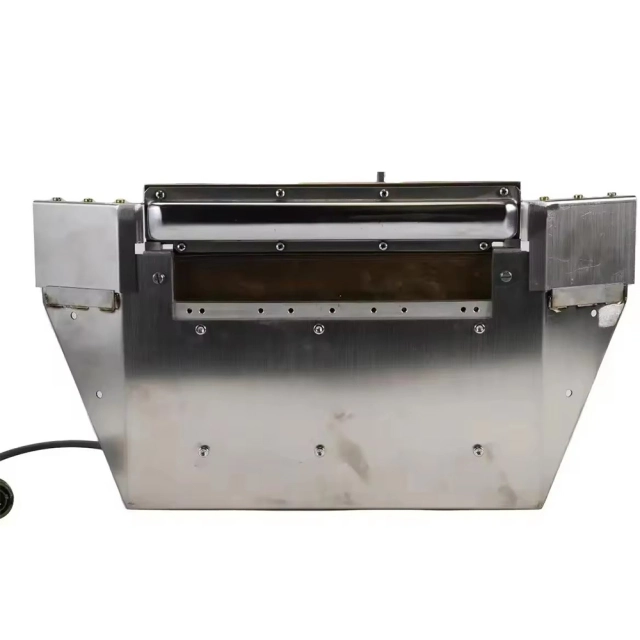
Comments
Post a Comment