How to Test and Optimize Fluorescent Pigment Performance in Your Manufacturing Process
Fluorescent pigments offer a vibrant and effective way to enhance the visual appeal and functionality of your products. However, achieving optimal performance requires careful testing and optimization within your specific manufacturing process. As a Fluorescent Pigment supplier, we understand the importance of consistent and reliable results. This blog provides a practical guide to testing and optimizing your Fluorescent Pigment performance, ensuring the best possible outcome for your applications.
Table of contents:
Step-by-Step Guide to Measuring Fluorescence Intensity and Wavelength Accuracy (Including 980nm)
Troubleshooting Common Issues: Dispersion Challenges in Water-Based vs. Solvent-Based Systems
Best Practices for Blending Fluorescent Pigments with Resins and Polymers
Step-by-Step Guide to Measuring Fluorescence Intensity and Wavelength Accuracy (Including 980nm)
Accurately measuring fluorescence intensity and wavelength accuracy is crucial for quality control. For pigments like IR980nm, which emit in the infrared spectrum, specialized equipment is necessary. Start by preparing a controlled sample of your pigment dispersed in the intended medium (resin, solvent, etc.). Use a spectrofluorometer to excite the sample with a specific wavelength and measure the emitted light. The spectrofluorometer will provide data on the intensity and wavelength of the emitted fluorescence. Ensure your instrument is properly calibrated and use consistent settings for each measurement. For IR980nm, confirm that your detector is sensitive in the 980nm range. Compare your measurements against the pigment supplier's specifications to verify the pigment's performance and identify any deviations. Consistent and accurate measurements are essential for identifying batch-to-batch variations and ensuring product consistency.
Troubleshooting Common Issues: Dispersion Challenges in Water-Based vs. Solvent-Based Systems
Proper dispersion is critical for achieving uniform color and optimal fluorescence. However, dispersion can be challenging, especially when working with different base systems. Water-based systems often require the use of surfactants or dispersants to prevent pigment agglomeration. Solvent-based systems may face challenges due to pigment polarity differences. If you observe streaking, settling, or reduced fluorescence intensity, it's likely due to poor dispersion. Experiment with different dispersants or adjust the mixing process to improve pigment distribution. Consider the pigment's surface treatment – some pigments are specifically treated for better compatibility with water-based or solvent-based systems. If you encounter persistent dispersion issues, consult with your Fluorescent Pigment supplier for tailored recommendations.
Best Practices for Blending Fluorescent Pigments with Resins and Polymers
The blending process significantly impacts the final performance of your fluorescent pigment. Start by carefully selecting the appropriate resin or polymer based on the pigment's compatibility and the desired end-product properties. Pre-dispersing the pigment in a small amount of the resin or a compatible solvent can help improve overall dispersion. Use a high-shear mixer to ensure uniform distribution of the pigment within the matrix. Avoid excessive heat during mixing, as high temperatures can degrade some pigments. The order of addition is also important – typically, the pigment should be added before any other additives. Thoroughly mix the components until a homogeneous blend is achieved. Regularly monitor the blend for consistency and adjust the process as needed to optimize the final product's appearance and performance.
Optimizing fluorescent pigment performance requires a systematic approach that includes accurate testing, effective dispersion techniques, and proper blending practices. By following these guidelines, you can maximize the impact of your pigments and achieve consistent, high-quality results in your manufacturing process. As a leading Fluorescent Pigment supplier, we are committed to providing you with the resources and support you need to succeed. Contact us today for expert advice and assistance in selecting and optimizing the right fluorescent pigments for your specific applications.
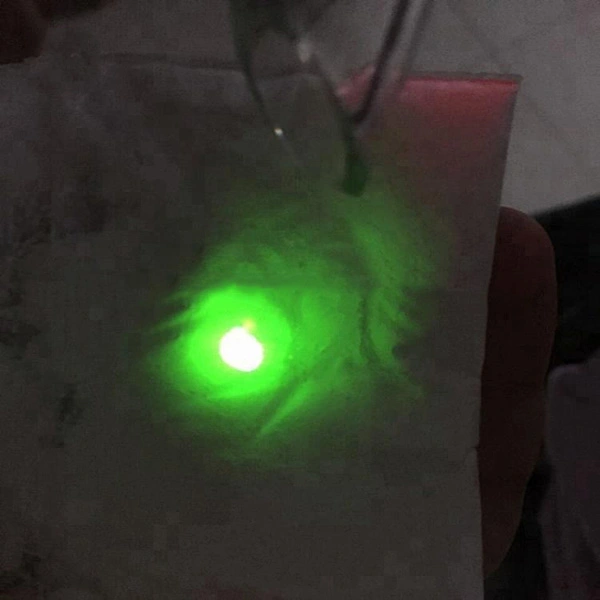
Comments
Post a Comment