Superior Properties of Inconel Alloys for Demanding Industries
Table of contents:
High-Temperature Resistance of Nickel Superalloys
Exceptional Corrosion Resistance in Harsh Environments
Mechanical Strength of Superalloy Bars for Critical Applications
Longevity and Durability of Inconel 718 Stock
High-Temperature Resistance of Nickel Superalloys
One of the most critical properties of any high-performance material is its ability to handle extreme heat without losing structural integrity. Nickel superalloys excel in this area, and Inconel 718, for example, is engineered to endure temperatures as high as 1300°F (700°C). This exceptional feature makes it a preferred choice for aerospace engine components, heat exchangers, and other systems exposed to high thermal stress. Using technology optimized by top-tier suppliers, such alloys maintain stability in both cryogenic and elevated temperature settings. This property ensures their suitability for applications that demand prolonged operation under intense heat, such as turbines and heat-treated equipment.
Exceptional Corrosion Resistance in Harsh Environments
Another defining characteristic of superalloys, such as nickel-based inconel alloys, is their exceptional resistance to corrosion. Industries handling aggressive chemical agents rely on materials that can withstand the degradation caused by such substances. Engineered with high nickel, chromium, and molybdenum content, superalloy bars fend off chloride stress corrosion, oxidation, and acidic environments effectively. Applications in chemical plants, marine systems, and energy sectors heavily utilize these materials to enhance system reliability. An additional advantage is their suitability in both oxidizing and reducing conditions, ensuring these materials maintain long-lasting durability. For harsh conditions, turning to established inconel suppliers guarantees that end products meet exacting industry standards.
Mechanical Strength of Superalloy Bars for Critical Applications
Performance is everything in engineering design, and superalloy bars lead in this arena. They exhibit incredible tensile strength, yield properties, and overall toughness. For instance, well-manufactured inconel 718 bars—the steelwork of choice for aerospace and gas turbine systems—are known for their robustness even when subjected to unimaginable pressure. The mechanical strength is a direct result of precise manufacturing processes that include heat treatments to strengthen the grain structure. Hence, whether in high-velocity wind tunnels or under crushing underwater pressures, superalloy bars ensure reliable performance with minimal wear and tear. Accessing such quality from reputed inconel 718 stockists ensures components meet performance benchmarks.
Longevity and Durability of Inconel 718 Stock
For industries requiring materials that stand the test of time, inconel alloys redefine longevity. Their combination of corrosion resistance, heat tolerance, and mechanical robustness reduces wear and failure rates, ensuring extended service life. This durability is especially critical for aerospace, power generation, and chemical processing facilities, where downtime incurs significant financial losses. Most importantly, the composition of inconel 718 stocks supports minimal degradation, even when exposed to highly fluctuating thermal and chemical stresses. Engineered to be steadfast over decades of use, they remain a cost-effective investment for industries prioritizing long-term reliability.
From their unmatched high-temperature resistance to superior mechanical performance, nickel superalloys like inconel answer the demands of cutting-edge industries. For companies searching for excellence, partnering with renowned inconel suppliers or sourcing via an inconel 718 stockist guarantees success in deploying reliable materials for engineering breakthroughs. Looking to source top-tier superalloy bars like inconel 718 for your next big project? Discover reliable, quality-assured options and upgrade your operations for unmatched performance today.
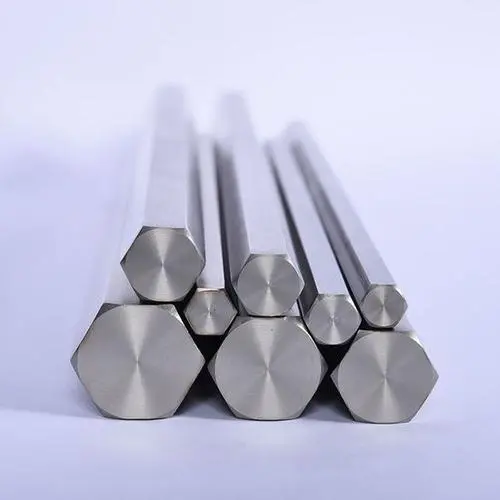
Comments
Post a Comment