Understanding the Metal Bipolar Plate Molding Production Line
Table of contents:
Overview of the Stamping Process
Cleaning, Welding, and Coating Procedures
Integration of MES and Intelligent Logistics Systems
Overview of the Stamping Process
The stamping process is the crucial initial stage in the production of metal bipolar plates, laying the foundation for their functionality in various applications, particularly fuel cells. This process involves the use of advanced molding techniques to create intricate and highly detailed designs with precise specifications that ensure optimal performance. The molds play a vital role in maintaining uniformity and accuracy, as even the slightest deviation could affect the efficiency of the bipolar plates. To achieve this, high-powered hydraulic presses, capable of generating nominal forces of up to 20,000 kN, are employed. These presses not only provide the necessary force to shape the metal but also enhance production efficiency through rapid stamping cycles. This minimizes production time, reduces costs, and maximizes throughput, enabling manufacturers to meet the growing demand for high-performance fuel cell components. Each step is meticulously controlled to ensure quality and reliability, making the stamping process an indispensable part of the manufacturing chain.
Cleaning, Welding, and Coating Procedures
After stamping, the plates go through a thorough cleaning process to remove any contaminants, such as oils, debris, or residues, ensuring a smooth, pristine surface for the next production steps. Advanced cleaning systems are employed, which can be customized to meet specific production requirements in terms of size and throughput, optimizing efficiency for large-scale manufacturing. Once cleaned, precision laser welding is used to join the stamped plates, creating complete bipolar plates. This process ensures a high level of accuracy, with laser welding providing exceptional consistency, strength, and durability in the welds. The use of high-quality materials, coupled with strict quality control standards, guarantees the reliability and longevity of the final product. After welding, the plates are subjected to a specialized surface treatment that enhances their resistance to corrosion, improves overall durability, and boosts performance in demanding environments, making them suitable for cutting-edge applications such as fuel cells and advanced energy systems.
Sealing and Testing Protocols
Sealing and testing are critical to guaranteeing the reliability and performance of metal bipolar plates used in fuel cells. High-quality sealing measures are meticulously implemented to ensure airtight conditions, which are essential for the efficient operation of fuel cells by preventing any gas leakage that could compromise performance. These sealing techniques often involve advanced materials and precision application methods to withstand varying operational conditions. In addition to sealing, rigorous testing protocols are conducted to evaluate strength, durability, and overall performance. These tests simulate real-world conditions, including exposure to extreme temperatures, pressure changes, and long-term usage, to ensure that each plate meets or exceeds industry standards. The testing process may also include chemical resistance assessments to confirm the plates' ability to function effectively in highly reactive environments. Such meticulous sealing and testing processes safeguard the plates' functionality and ensure their long-term reliability across a range of fuel cell applications, from portable devices to large-scale energy systems. This comprehensive approach provides users with confidence in the performance and durability of their fuel cell systems.
Integration of MES and Intelligent Logistics Systems
The Metal Bipolar Plate Molding Production Line incorporates advanced Manufacturing Execution Systems (MES) and intelligent logistics systems for optimal workflow management. MES systems offer real-time monitoring and control of the production process, ensuring that every step runs smoothly. Intelligent logistics further streamline material handling, feeding operations, and discharge processes. With precision feeding systems allowing accuracies of ±0.2 mm/m and discharge line speeds of up to 16 m/min, productivity is enhanced, reducing delays and ensuring seamless operation.
The Metal Bipolar Plate Molding Production Line embodies state-of-the-art technology and innovation. Its advanced processes, from stamping to testing, combined with automation through MES and intelligent logistics, make it a critical tool for manufacturers in the fuel cell industry. It not only supports high-volume, quality production but also accelerates the adoption of sustainable energy solutions. If you’re looking to enhance your fuel cell production capabilities, the Metal Bipolar Plate Molding Production Line delivers the precision, efficiency, and reliability you need.
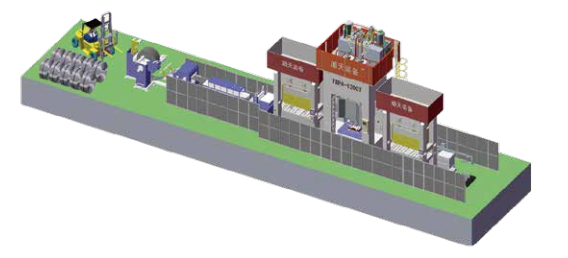
Comments
Post a Comment